Nanofiber Architectures: Tailoring Structure and Function
The creation and study of nanofibers have gotten a lot of interest because they have special features and could be used in many areas, such as biomedical engineering, filtration, and composite materials. Electrospinning and self-assembly are the two main ways to make nanofibers. Each has its own benefits when it comes to controlling the fiber’s shape and chemical makeup.
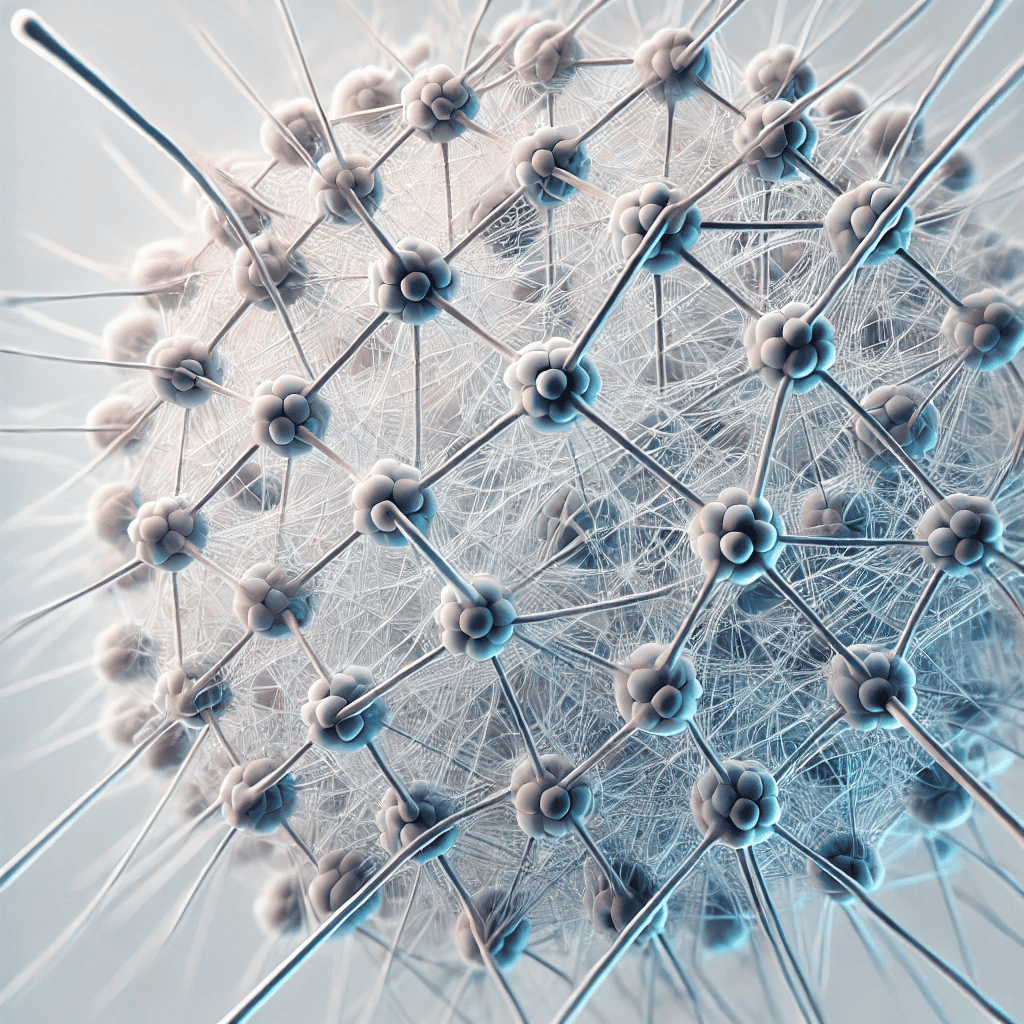
Electrospinning is a common method that uses a strong electric field to spin polymer solutions or melts into very thin strands with diameters in the nanometer range. This technique makes it possible to make long nanofibers with a lot of surface area compared to volume, which is very important for uses like tissue engineering and drug transport (Leung & Ko, 2010; Wang et al., 2015). You can improve the electrospinning process by changing things like the solution viscosity, the strength of the electric field, and the distance between the collectors. These changes have a direct effect on the shape and mechanical qualities of the nanofibers that are made (Pan et al., 2010; Qiang et al., 2013). For example, aligning nanofibers during electrospinning can make their mechanical qualities better. This has been shown by studies that show big increases in tensile strength and modulus for structures that are aligned (Hooshmand et al., 2015; Sensini et al., 2021).
On the other hand, self-assembly is when molecules arrange themselves into ordered patterns on their own, without any help from outside sources. This method works great for making nanofibers from biopolymers like chitin and cellulose, which can then be changed to make them more useful (Ifuku & Saimoto, 2012; Ifuku et al., 2011). Surface functionalization methods, like adding nanoparticles or changing the chemicals, can change the nanofibers’ features even more, making them better at being biocompatible and strong (Bocková et al., 2022; Tanaka et al., 2017). A good example is adding magnetic nanoparticles to polymer nanofibers has been shown to make them more useful for drug transport and cleaning up the environment (Tanaka et al., 2017).
Morphological control techniques are very important for figuring out how well nanofibers work and how strong their structures are. Some of the most important things that determine the mechanical qualities of nanofibers are their diameter, porosity, and alignment. Research has shown that a smaller fiber diameter means a bigger surface area. This can make it easier for the fiber to connect with living tissues in biomedical settings (Zakaria & Nakane, 2019; Misslitz et al., 2012). Additionally, the porosity of nanofiber mats can be changed to achieve the desired filter rates, as higher porosity usually means better particle capture (Misslitz et al., 2012; Selatile et al., 2021).
To understand how nanofibers’ structure and properties are related, we need to use advanced characterization methods. Some tools, like scanning electron microscopy (SEM), transmission electron microscopy (TEM), and atomic force microscopy (AFM), help us understand the shape of nanofibers. Other tools, like mechanical testing, check their tensile strength and elasticity (Conte et al., 2020; Nakashima et al., 2011). Also, thermal analysis methods like differential scanning calorimetry (DSC) and thermogravimetric analysis (TGA) are used to check how stable and how quickly nanofibers break down at high temperatures, which is important for their use in those conditions (Tian & He, 2022; Aduba et al., 2013).
Creating and studying nanofibers through electrospinning and self-assembly is a flexible way to make materials with specific qualities that can be used in a wide range of situations. The way that morphological control, chemical composition, and advanced characterization methods work together is a key part of improving the performance of nanofibers and making them more useful in areas like medicine, filtration, and environmental science.
References
Aduba, D., Hammer, J., Yuan, Q., Yeudall, W., Bowlin, G., & Yang, H. (2013). Semi-interpenetrating network (sipn) gelatin nanofiber scaffolds for oral mucosal drug delivery. Acta Biomaterialia, 9(5), 6576-6584. https://doi.org/10.1016/j.actbio.2013.02.006
Bocková, M., Pashchenko, A., Stuchlíková, S., Kalabova, H., Divín, R., Novotný, P., … & Hoch, J. (2022). Low concentrated fractionalized nanofibers as suitable fillers for optimization of structural–functional parameters of dead space gel implants after rectal extirpation. Gels, 8(3), 158. https://doi.org/10.3390/gels8030158
Conte, A., Sun, K., Hu, X., & Beachley, V. (2020). Effects of fiber density and strain rate on the mechanical properties of electrospun polycaprolactone nanofiber mats. Frontiers in Chemistry, 8. https://doi.org/10.3389/fchem.2020.00610
Hooshmand, S., Aitomäki, Y., Norberg, N., Mathew, A., & Oksman, K. (2015). Dry-spun single-filament fibers comprising solely cellulose nanofibers from bioresidue. Acs Applied Materials & Interfaces, 7(23), 13022-13028. https://doi.org/10.1021/acsami.5b03091
Ifuku, S. and Saimoto, H. (2012). Chitin nanofibers: preparations, modifications, and applications. Nanoscale, 4(11), 3308-3318. https://doi.org/10.1039/c2nr30383c
Ifuku, S., Nomura, R., Morimoto, M., & Saimoto, H. (2011). Preparation of chitin nanofibers from mushrooms. Materials, 4(8), 1417-1425. https://doi.org/10.3390/ma4081417
Leung, V. and Ko, F. (2010). Biomedical applications of nanofibers. Polymers for Advanced Technologies, 22(3), 350-365. https://doi.org/10.1002/pat.1813
Misslitz, H., Kreger, K., & Schmidt, H. (2012). Supramolecular nanofiber webs in nonwoven scaffolds as potential filter media. Small, 9(12), 2053-2058. https://doi.org/10.1002/smll.201202334
Nakashima, R., Watanabe, K., Lee, Y., Kim, B., & Kim, I. (2011). Mechanical properties of poly(vinylidene fluoride) nanofiber filaments prepared by electrospinning and twisting. Advances in Polymer Technology, 32(S1). https://doi.org/10.1002/adv.20268
Pan, W., He, X., & Chen, Y. (2010). Preparation and characterization of polyacrylonitrile-polyaniline blend nanofibers. Applied Mechanics and Materials, 44-47, 2195-2198. https://doi.org/10.4028/www.scientific.net/amm.44-47.2195
Qiang, J., Wan, Y., Yang, L., & Cao, Q. (2013). Effect of ultrasonic vibration on structure and performance of electrospun pan fibrous membrane. Journal of Nano Research, 23, 96-103. https://doi.org/10.4028/www.scientific.net/jnanor.23.96
Selatile, K., Ray, S., Ojijo, V., & Sadiku, R. (2021). Morphological, thermal, and mechanical properties of electrospun recycled poly(ethylene terephthalate)/graphene oxide composite nanofiber membranes. Acs Omega, 6(32), 21005-21015. https://doi.org/10.1021/acsomega.1c02578
Sensini, A., Santare, M., Eichenlaub, E., Bloom, E., Gotti, C., Zucchelli, A., … & Cristofolini, L. (2021). Tuning the structure of nylon 6,6 electrospun bundles to mimic the mechanical performance of tendon fascicles. Frontiers in Bioengineering and Biotechnology, 9. https://doi.org/10.3389/fbioe.2021.626433
Tanaka, K., Okada, T., Motohashi, Y., & Katayama, T. (2017). Fabrication of magnetite/pla composite nanofiber sheet and evaluation of its mechanical properties.. https://doi.org/10.2495/mc170271
Tian, D. and He, J. (2022). Macromolecular-scale electrospinning controlling inner topologic structure through a blowing air. Thermal Science, 26(3 Part B), 2663-2666. https://doi.org/10.2298/tsci2203663t
Wang, A., Xu, C., Zhang, C., Ye, G., & Wang, B. (2015). Experimental investigation of the properties of electrospun nanofibers for potential medical application. Journal of Nanomaterials, 2015(1). https://doi.org/10.1155/2015/418932
Zakaria, M. and Nakane, K. (2019). Fabrication of polypropylene nanofibers from polypropylene/polyvinyl butyral blend films using laser‐assisted melt‐electrospinning. Polymer Engineering & Science, 60(2), 362-370. https://doi.org/10.1002/pen.25291