Recent Developments in 3D Printed Microfluidics
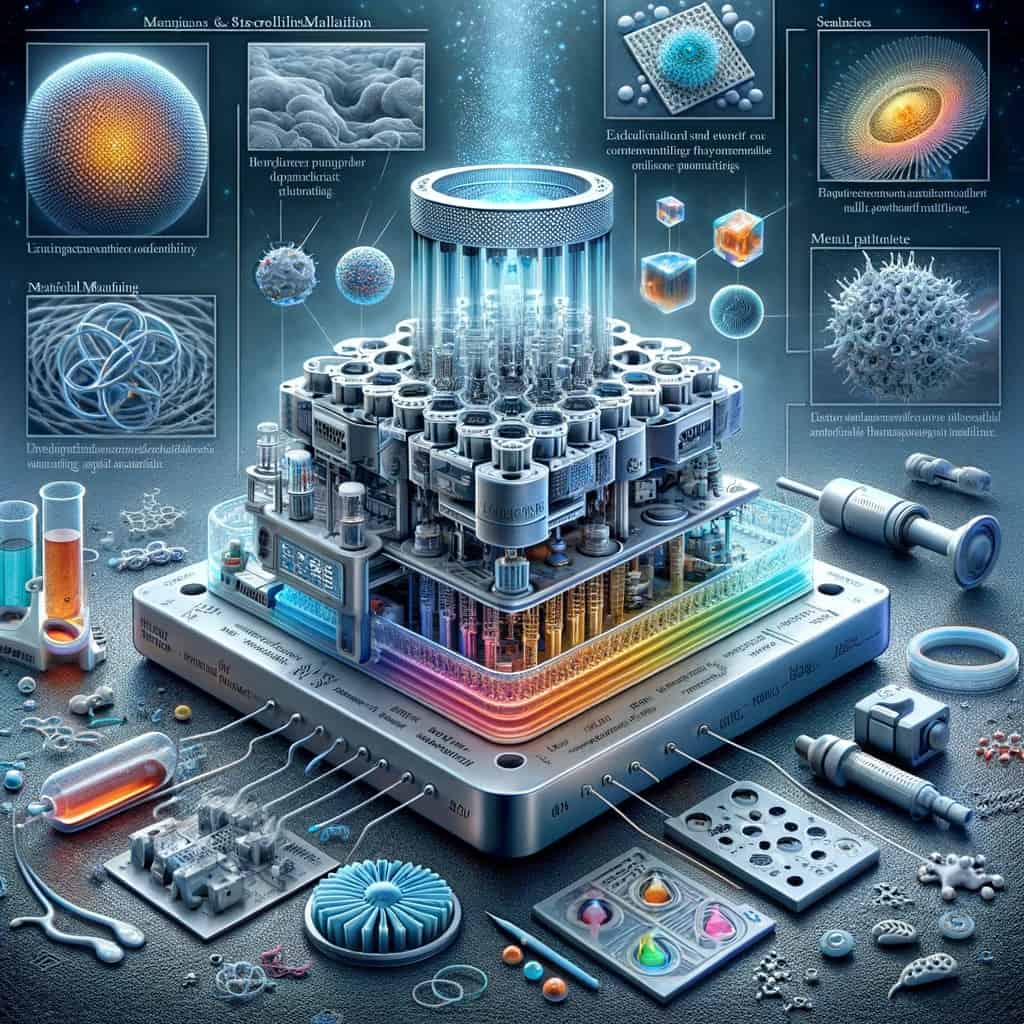
An Overview of 3D Printed Microfluidic Systems
The field of microfluidics deals with the manipulation of fluids on a very small scale, usually in the microliter or nanoliter range. In order to carry out diverse activities like chemical reactions, sample analysis, and cell investigations, it requires accurate control and manipulation of fluids within microchannels (Convery et al., 2021). Because it can miniaturize and integrate complex laboratory functions onto a single chip, this technology has significant applications in a variety of fields, including biology, chemistry, and medicine. This leads to advantages like reduced sample volumes, faster reaction times, and increased automation (Alapan et al., 2015). 3D printing technology has become an effective and adaptable tool for fabricating microfluidic devices. Microfluidic devices are frequently made using a variety of 3D printing processes, including selective laser sintering (SLS), fused deposition modeling (FDM), and stereolithography (SLA) (Männel et al., 2021). Regarding resolution, material compatibility, and production speed, each of these methods has a distinct edge. For example, SLA may be used to create complex microfluidic structures because of its high resolution and surface smoothness, whereas FDM can produce larger devices more affordably and quickly through rapid prototyping (Romanov et al., 2018). There are various advantages to fabricating microfluidic devices using 3D printing. Customization is a major benefit, since researchers may effortlessly create and manufacture gadgets that are suited to certain experimental requirements (Balakrishnan et al., 2020). Advanced applications like droplet microfluidics for high-throughput screening and single-cell analysis are made possible by this customization, which enables the integration of complicated geometries and capabilities inside the microfluidic system (Männel et al., 2021). Furthermore, quick prototyping is made possible by 3D printing, which lowers the time and expense associated with iterating designs and testing various configurations (Kabandana et al., 2020). The performance and utility of microfluidic devices are increased by the capacity to design complex structures, such as micromixers and valves, which improves fluid control and mixing efficiency (Noriega et al., 2021). Additionally, the integration of several materials with different properties into a single microfluidic chip is made possible by 3D printing, which makes it possible to incorporate stiff and flexible components for a variety of functions (Ahmed et al., 2022). This feature broadens the range of applications for microfluidic devices and increases their adaptability to diverse research domains. Additionally, 3D-printed microfluidic devices are now more durable and adaptable due to the development of novel materials and printing techniques like transparent resins and high-pressure, heat-resistant polymers, which have addressed issues with device transparency, chemical compatibility, and operating conditions (Sreenivasan et al., 2020). To sum up, the integration of 3D printing and microfluidics technology has transformed the field of lab-on-a-chip systems, providing researchers with robust instruments to perform an extensive array of biological, chemical, and medicinal studies. Innovation and discovery in a wide range of scientific fields are now possible due to the quick and affordable fabrication of customized, complicated microfluidic devices.
Developments in 3D Printed Microfluidics Technology
Materials for 3D Printed Microfluidic Devices: A wide range of materials are used in the field of 3D printing for microfluidic devices in order to meet the unique needs of microfluidic applications. These materials include composites, polymers, and resins; each of these materials has unique qualities that are essential to the functioning of microfluidic systems (Descamps et al., 2021). Polycarbonate (PC), polymethylmethacrylate (PMMA), and cyclic olefin copolymer (COC) are thermoplastic polymers that are frequently utilized because they work well with microfluidic and lab-on-a-chip technologies (Fu et al., 2019). These materials are perfect for a variety of microfluidic applications because they strike a compromise between transparency, chemical resistance, and ease of production. 3D Printing Innovations for Enhanced Microfluidic Functionality: The functionality of 3D printed microfluidic devices has been greatly improved by recent technological developments. In order to provide accurate control and automation of operations, integrated sensors have been created that allow for real-time monitoring of multiple parameters within microfluidic systems (Begolo et al., 2014). In order to improve fluid control and mixing efficiency, high-resolution printing techniques have been improved to create finer channels and complex structures within microfluidic devices. Furthermore, complex, multi-functional microfluidic systems that combine stiff and flexible components for a variety of applications have been created by utilizing multi-material printing capabilities. These developments have opened up new avenues for research in biology, chemistry, and medicine by pushing the area of 3D printed microfluidics towards greater variety and sophistication. Problems and Solutions: Even with the advancements in 3D printed microfluidics, a number of problems still exist that call for creative fixes. Surface smoothness is still important because rough surfaces can cause flow disturbances in microfluidic channels and sample adherence. To enhance surface quality and lessen surface roughness, sophisticated post-processing methods such solvent smoothing and surface coating have been developed (Miles et al., 2019). Another important consideration is biocompatibility, particularly for applications involving biological samples or cells. To improve biocompatibility and reduce harmful effects on living entities, researchers are looking into bioresorbable polymers and surface changes (Descamps et al., 2021). The introduction of novel bonding techniques, such as solvent bonding and plasma treatment, has addressed bonding difficulties, such as poor adhesion between layers in 3D printed microfluidic devices, providing robust and leak-free device assembly. In conclusion, the discipline of 3D printed microfluidics is moving toward increased functionality, customisation, and reliability as a result of material advancements, technological advancements, and answers to current problems. Through the utilization of a wide variety of materials, the integration of sophisticated functionalities such as sensors and multi-material printing, and the creative resolution of significant obstacles, scientists are expanding the frontiers of microfluidic device manufacturing and use.
Uses for 3D Printing Microfluidics
Healthcare and Diagnostics: By offering cutting-edge solutions in a number of fields, including point-of-care diagnostics, customized medicine, and organ-on-a-chip models for drug testing, 3D printed microfluidic devices have had a substantial impact on the healthcare industry. These tools make it possible to quickly and affordably create unique microfluidic systems that are suited for certain medicinal uses. Gong and associates (2017). According to Plevniak et al. (2016), 3D printed microfluidics makes it possible to create portable, user-friendly diagnostic instruments for the rapid and precise analysis of biological samples in point-of-care diagnostics. This results in prompt medical interventions and better patient outcomes. The development of microfluidic devices, which can mimic the physiological conditions of specific patients and enable precise drug administration and treatment techniques, is advantageous for personalized medicine (Prabhakar et al., 2021). Organ-on-a-chip models are more accurate and efficient than existing approaches for drug screening and toxicity assessment because they replicate the microenvironment of human organs thanks to 3D printed microfluidics (Jo et al., 2022). These developments in medical technology demonstrate the revolutionary potential of 3D printed microfluidic devices to improve drug research, therapy, and diagnosis procedures. Environmental Monitoring: To assess water quality and analyze air pollution, environmental monitoring must make use of 3D printed microfluidics. According to Bilatto et al. (2017), these gadgets offer lightweight and efficient platforms for environmental parameter testing and monitoring on-site. According to Bickham et al. (2020), 3D printed microfluidic devices have the ability to identify infections, contaminants, and chemical pollutants in water sources. This allows for a quick and accurate examination to guarantee the safety of the water. Microfluidic systems with sensors incorporated may detect and quantify pollutants in real-time for air pollution studies, providing useful information for evaluating air quality and putting pollution control measures in place (Shin et al., 2022). Because of their adaptability and scalability, 3D printed microfluidics are useful instruments for environmental monitoring applications, supporting efforts to safeguard the environment and public health. upcoming prospects: Future developments in 3D printed microfluidics have the potential to significantly advance innovation and research in a number of different disciplines. The goal of ongoing research is to improve these devices’ performance and functionality by including biosensors, multi-material printing capabilities, and high-resolution printing for finer channels (Macdonald et al., 2017). The creation of innovative materials and manufacturing processes to solve contemporary problems including surface smoothness, biocompatibility, and bonding problems are examples of emerging potential (Kecili & Tekin, 2020). Furthermore, it’s expected that the pursuit of novel applications in disciplines like environmental science, healthcare, and materials research would propel advancements in 3D printed microfluidics (Prabhakar et al., 2021). Researchers and practitioners will likely be able to fabricate microfluidic devices more easily as a result of the ongoing advancements in 3D printing technology and their increased accessibility, opening up new avenues for scientific and technological inquiry (Knowlton et al., 2016). All things considered, the future of 3D printed microfluidics seems bright, with the potential to transform a variety of sectors and open the door to ground-breaking discoveries and inventions.
References:
Ahmed, I., Sullivan, K., & Priye, A. (2022). Multi-resin masked stereolithography (msla) 3d printing for rapid and inexpensive prototyping of microfluidic chips with integrated functional components. Biosensors, 12(8), 652. https://doi.org/10.3390/bios12080652
Alapan, Y., Hasan, M., Shen, R., & Gurkan, U. (2015). Three-dimensional printing based hybrid manufacturing of microfluidic devices. Journal of Nanotechnology in Engineering and Medicine, 6(2). https://doi.org/10.1115/1.4031231
Balakrishnan, H., Badar, F., Doeven, E., Novak, J., Merenda, A., Dumée, L., … & Guijt, R. (2020). 3d printing: an alternative microfabrication approach with unprecedented opportunities in design. Analytical Chemistry, 93(1), 350-366. https://doi.org/10.1021/acs.analchem.0c04672
Begolo, S., Zhukov, D., Selck, D., Li, L., & Ismagilov, R. (2014). The pumping lid: investigating multi-material 3d printing for equipment-free, programmable generation of positive and negative pressures for microfluidic applications. Lab on a Chip, 14(24), 4616-4628. https://doi.org/10.1039/c4lc00910j
Bickham, A., Pang, C., George, B., Topham, D., Nielsen, J., & Nordin, G. (2020). 3d printed microfluidic devices for solid-phase extraction and on-chip fluorescent labeling of preterm birth risk biomarkers. Analytical Chemistry, 92(18), 12322-12329. https://doi.org/10.1021/acs.analchem.0c01970
Bilatto, S., Adly, N., Correa, D., Wolfrum, B., Offenhäusser, A., & Yakushenko, A. (2017). Printed microfluidic filter for heparinized blood. Biomicrofluidics, 11(3). https://doi.org/10.1063/1.4982963
Convery, N., Samardzhieva, I., Stormonth-Darling, J., Harrison, S., Sullivan, G., & Gadegaard, N. (2021). 3d printed tooling for injection molded microfluidics. Macromolecular Materials and Engineering, 306(11). https://doi.org/10.1002/mame.202100464
Descamps, L., Roy, D., Tomba, C., & Deman, A. (2021). Magnetic polymers for magnetophoretic separation in microfluidic devices. Magnetochemistry, 7(7), 100. https://doi.org/10.3390/magnetochemistry7070100
Fu, G., Zhu, Y., Wang, W., Zhou, M., & Li, X. (2019). Spatiotemporally controlled multiplexed photothermal microfluidic pumping under monitoring of on-chip thermal imaging. Acs Sensors, 4(9), 2481-2490. https://doi.org/10.1021/acssensors.9b01109
Gong, H., Bickham, B., Woolley, A., & Nordin, G. (2017). Custom 3d printer and resin for 18 μm × 20 μm microfluidic flow channels. Lab on a Chip, 17(17), 2899-2909. https://doi.org/10.1039/c7lc00644f
Jo, B., Morimoto, Y., & Takeuchi, S. (2022). 3d‐printed centrifugal pump driven by magnetic force in applications for microfluidics in biological analysis. Advanced Healthcare Materials, 11(24). https://doi.org/10.1002/adhm.202200593
Kabandana, G., Jones, C., Sharifi, S., & Chen, C. (2020). 3d-printed microfluidic devices for enhanced online sampling and direct optical measurements. Acs Sensors, 5(7), 2044-2051. https://doi.org/10.1021/acssensors.0c00507
Kecili, S. and Tekin, H. (2020). Adhesive bonding strategies to fabricate high-strength and transparent 3d printed microfluidic device. Biomicrofluidics, 14(2). https://doi.org/10.1063/5.0003302
Knowlton, S., Yu, C., Ersoy, F., Emadi, S., & Khademhosseini, A. (2016). 3d-printed microfluidic chips with patterned, cell-laden hydrogel constructs. Biofabrication, 8(2), 025019. https://doi.org/10.1088/1758-5090/8/2/025019
Macdonald, N., Cabot, J., Šmejkal, P., Guijt, R., Paull, B., & Breadmore, M. (2017). Comparing microfluidic performance of three-dimensional (3d) printing platforms. Analytical Chemistry, 89(7), 3858-3866. https://doi.org/10.1021/acs.analchem.7b00136
Miles, M., Bhattacharjee, B., Sridhar, N., Fajrial, A., Ball, K., Lee, Y., … & Ding, X. (2019). Flattening of diluted species profile via passive geometry in a microfluidic device. Micromachines, 10(12), 839. https://doi.org/10.3390/mi10120839
Männel, M., Baysak, E., & Thiele, J. (2021). Fabrication of microfluidic devices for emulsion formation by microstereolithography. Molecules, 26(9), 2817. https://doi.org/10.3390/molecules26092817
Noriega, J., Chartrand, N., Valdoz, J., Cribbs, C., Jacobs, D., Poulson, P., … & Nordin, G. (2021). Spatially and optically tailored 3d printing for highly miniaturized and integrated microfluidics. Nature Communications, 12(1). https://doi.org/10.1038/s41467-021-25788-w
Plevniak, K., Campbell, M., Myers, T., Hodges, A., & He, M. (2016). 3d printed auto-mixing chip enables rapid smartphone diagnosis of anemia. Biomicrofluidics, 10(5). https://doi.org/10.1063/1.4964499
Prabhakar, P., Sen, R., Dwivedi, N., Khan, R., Solanki, P., Srivastava, A., … & Dhand, C. (2021). 3d-printed microfluidics and potential biomedical applications. Frontiers in Nanotechnology, 3. https://doi.org/10.3389/fnano.2021.609355
Romanov, V., Samuel, R., Chaharlang, M., Jafek, A., Frost, A., & Gale, B. (2018). Fdm 3d printing of high-pressure, heat-resistant, transparent microfluidic devices. Analytical Chemistry, 90(17), 10450-10456. https://doi.org/10.1021/acs.analchem.8b02356
Shin, S., Park, G., Kim, W., & So, H. (2022). A hybrid fabrication technique of capacitive flow meters using three-dimensional printing for rectifying airflows. Ieee Access, 10, 45073-45079. https://doi.org/10.1109/access.2022.3165428
Sreenivasan, P., Wilson, J., Nair, P., & Thomas, L. (2020). Polycaprolactone solution–based ink for designing microfluidic channels on paper via 3d printing platform for biosensing application. Polymers for Advanced Technologies, 31(5), 1139-1149. https://doi.org/10.1002/pat.4848